SLABlite In The News
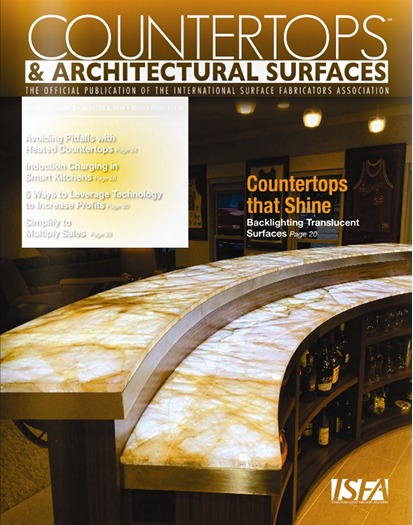
SLABlite was recently featured in an article by Countertops & Architectural Surfaces, Volume 7, Issue 3. This publication is an official product of the International Surface Fabricators Association and focuses heavily on technological advancements in the countertop industry. The magazine features and article on backlighting and you can read the article in its entirety here.
“A growing number of the premium surfacing materials on the market today have versions that feature translucency. And to take full advantage of that quality requires the use of backlighting. Natural onyx has always been seen as a product that really shows its spectacular depth when lit from behind, but now the list of materials that can benefit from backlighting includes a variety of solid surfaces (such as Avonite’s Glass Series), engineered stones (such as Cosentino’s Prexury made of semi-precious stones) and certain quartz surfacing, like Vicostone’s Chalcedony). And, of course, glass and glass-based conglomerate materials are also well suited for backlighting.
Lighting these materials from behind greatly enhances their natural beauty. The effect can transport the mood of a room from just nice to spectacular. The “wow factor” is incredible. Done correctly, light adds dimension and depth. It allows the viewer to not only see the lovely surface, but also see into the material, giving each installation the one-of-a-kind aspect that is so desirable today. People are literally stunned when they see these materials lit from behind.
Early Methods
Through the years, many approaches to backlighting have been attempted, with varying degrees of success and problems. Light boxes using fluorescent lamps or light bulbs were among the first methods attempted.
When using light boxes, because of the modular nature of cabinets, a series of them would have to be built to fit the modular framework. For this method to work at all, a minimum of 4 in. of space was needed between the countertop and the light source to diminish hotspots and shadows. And even with that space built in, illumination was still not smooth and even. Shadows at the edges of the boxes and striping where the fluorescent lamps were situated could not be avoided (see Figure 1). Additionally, it was impossible to light areas around sinks and counter overhangs. Even, edge-to-edge lighting just was not possible, and 4 in. of valuable cabinet space was lost in the process. This led many to conclude that light boxes were not the best solution to bringing out the true beauty of translucent material.
So, some fabricators tried using Christmas tree lights to spread out the light more evenly, but while smaller, there were still shadows and hot spots and overhangs could not be lit. Then, with the advent of LED lighting, some tried LED pucks or rope lighting to try to more evenly light their countertops. Unfortunately, they found that any type of rope lighting created a snake-like effect. LED pucks or panels with LEDs spread across the surface gave the effect of spots of light across the top. And with these methods lighting the edge of the countertop gave a halo effect.
To evenly light countertops, the light source has to cover the countertop completely. It has to be able to be on top of the support of the modular cabinets, to be around the sink and the overhang. If this is not possible, the countertop will be shadowed, taking away from the intrinsic beauty of the material.
New Times, New Methods
The invention of the light guide revolutionized the way features can be illuminated. A relatively new concept, a light guide is similar to what is used in cell phone screens, computer monitors or LED televisions.
Some suppliers of these light guides (often called LED panels) custom fit them for a specific application, while others offer panels that can be custom cut on site, allowing the installer to cut and shape the light guides to fit around the sink and stove as well. This eliminates the need for templates and trips back to the shop to cut and shape the lighting or waiting for custom-sized panels to be made and shipped.
And, if done correctly, the finished piece should look as natural as if the sun was shining through it, with no hot spots or shadowing.
Custom Residential Quartzite Bar
Stonesmith has been in business for 12 years and has 15 employees. The company works with a variety of materials, such as granite, marble, quartz surfacing, solid surface and more. It partners with large custom builders and high-end remodelers, performing both commercial and residential jobs.
A prime example of how trouble-free this type of application can be using light guides is a residential project performed by fabricator Stonesmith Inc, in Carrollton, Texas.
Rick Zuppa, project manager for Stonesmith, has been a fabricator since 1995, but never tackled a backlighting project until the company was hired to create a custom, two-tier radius bar using 3cm natural quartz slab material (see Figure 4). The material, provided by IMC, was in the color Lumix, which has the translucent properties of quartz crystals interspersed with light brown veins and patches of minerals.
were cut to size on the jobsite and placed on top of the bar. Then the top was installed over the light panels without difficulty. “This was our first residential backlighting project,” said Zuppa. “But the process was very simple and we didn’t really do anything out of the ordinary to finish the project.”
The bar tops were templated and fabricated in the usual fashion, and a light guide system was used for the backlighting (in this case the SLABlite light guide system). Before the stone top was installed, the guide lights were cut to size on the jobsite and placed on top of the bar. Then the top was installed over the light panels without difficulty. “This was our first residential backlighting project,” said Zuppa. “But the process was very simple and we didn’t really do anything out of the ordinary to finish the project.”
“The finished product looked awesome,” he explained, “and the lighting really brought out all of the beauty of this material. Now, we are starting to see more [backlit applications] on the commercial level as well. It’s a great way to show off how unique and different all of these [translucent] materials are.”
Overcoming the Challenges
Of course, not all light guides are the same and not all transparent material will light exactly the same as the next. However, there are some tricks to getting the best results from a given material. As a rule of thumb, materials that are thicker, have more color and/or are more opaque are generally easier to backlight. Materials such as honey onyx, natural quartzite, and thicker engineered stones (such as Caesarstone’s Concetto or Cosentino’s Prexury) are pretty easy to light using light guides. They are full of crystals that not only impart unique beauty, but also allow the light to bounce around inside the slab, by putting down 1 in. clear acrylic square rod as spacers.
Making up for the additional step when using white colors of these more translucent materials is the fact that you can use RGB LED lights to make them any color you desire, or even change colors.
A Few Last Pointers
A new era in illumination is here. Only the boundaries of your imagination will limit what can be done and the ways the science can be applied. But, before going out and jumping head-first into the realm of backlit surfaces, there are a couple of things to keep in mind.
First, when selecting a countertop lighting system, it is important to use only sealed or encapsulated LED light panels. This prevents moisture from damaging the lights under the countertop, a mandatory requirement for kitchen and bath use. Also take note of how the light panels are encapsulated. If only the LEDs are potted in plastic, they could potentially separate from the plastic allowing the LEDs to be exposed to the elements. It is best if the light guide in its entirety is encapsulated, not just the LEDs.
And, check for a warranty. This is definitely a situation where a little more spent for a quality light system pays off handsomely in the long run. A properly encapsulated, low-voltage LED light panel lets off almost no heat and can last for 20 years or more. However, the cost of a call-back for faulty lighting can easily kill any additional profit from taking on a backlit surfacing project in the first place. So while showing off just what can be done is a great benefit, in the end also has to be profitable.
Richard Ashoff is CEO of TylerCo Inc., Irvine, Calif., the provider of SLABlite backlighting panels. More information is available at www.tylercoinc.com or by contacting Ashoff at (877) 723-2900 or r.ashoff@tylercoinccdev.wpenginepowered.com.